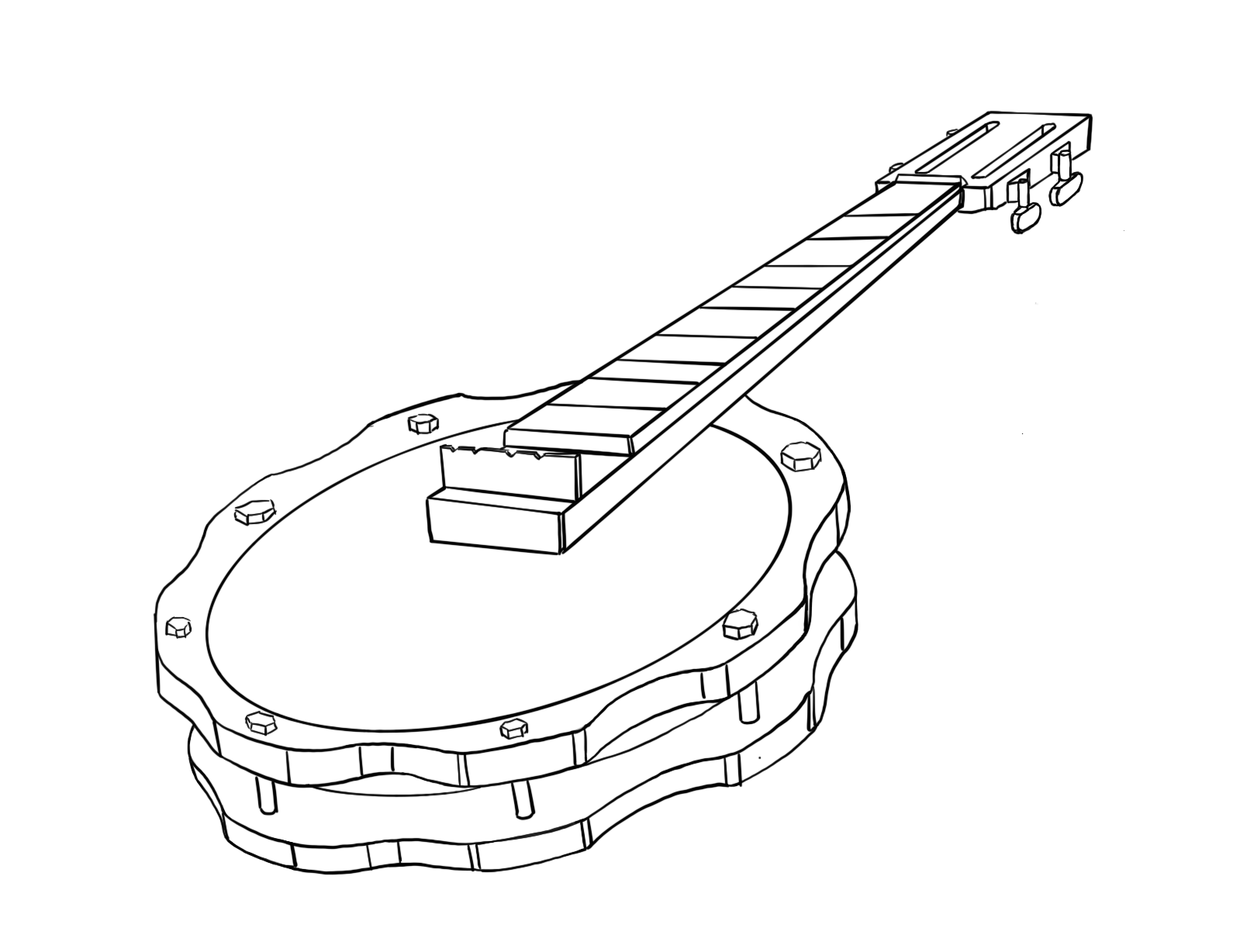
Goal:
As part of Music Instrument Design and Manufacturing course this semester, I was tasked to build a ukulele. The goal of this project was, given a strung CNC cut neck, we were to build a resonating cavity in order to produce the longest RT60. RT60 is the time it takes for a single pluck to decay to 60% of its original amplitude.
Final Product:
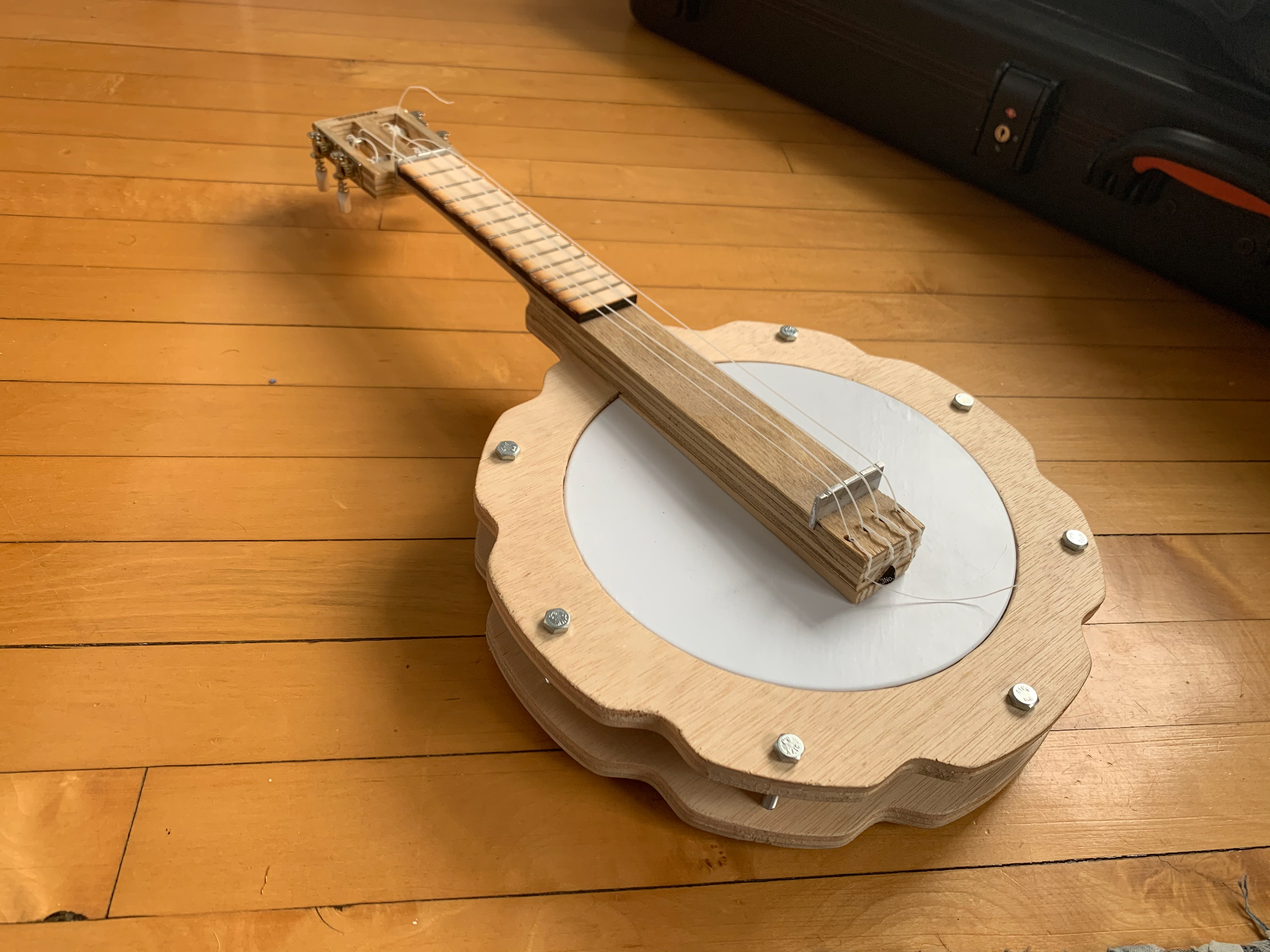
Approach:
After an initial round of sketching and ideation, my group settled on attempting to make a ukulele banjo mashup utilizing the Vacuum-former and CNC at the Shop.
After a rough remodel of the Banjolele in Solidworks, I created a final assembly, seen below, to grab a visualization of the final product.
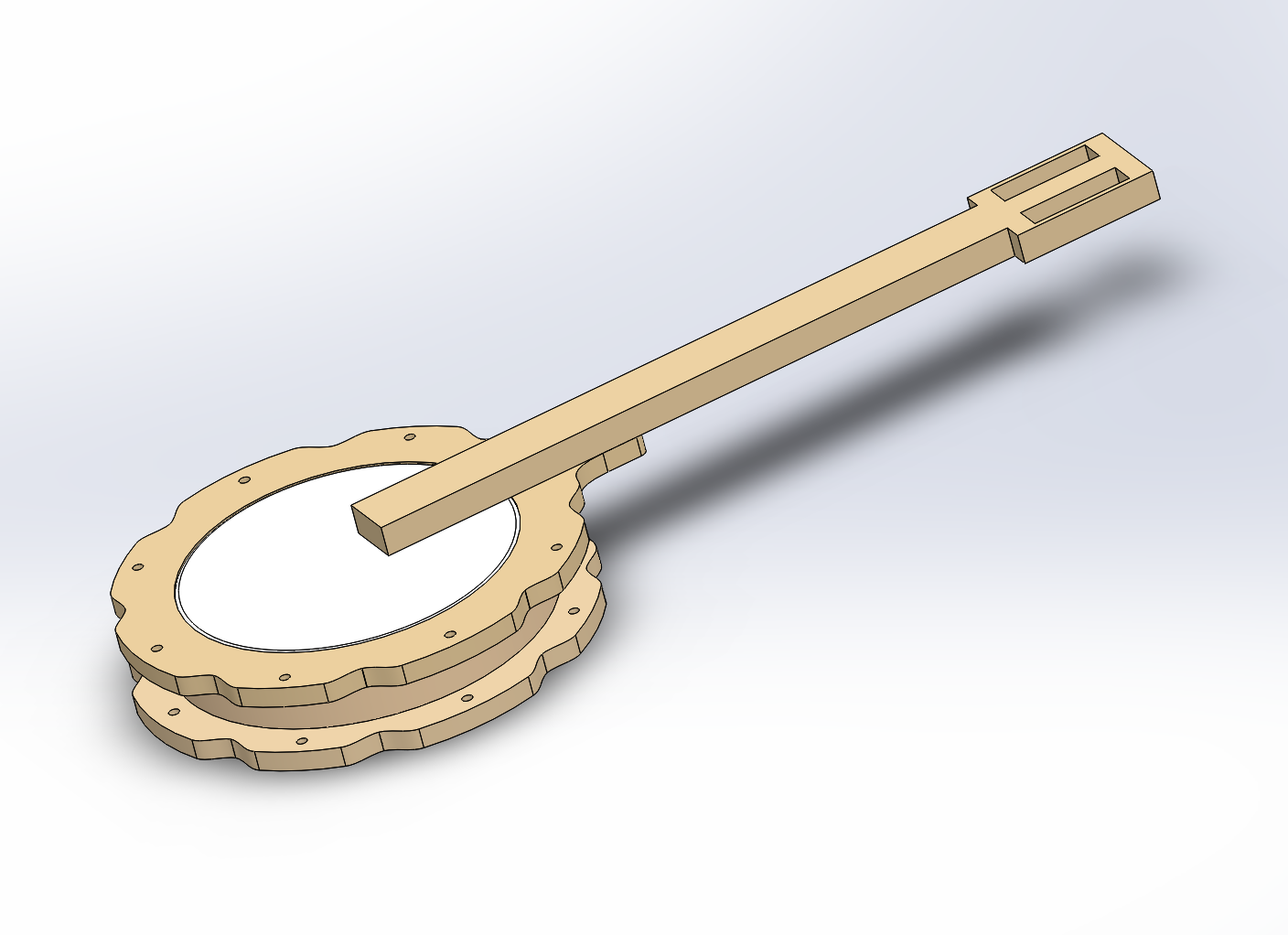
Exporting each of the assembly components we first focused on manufacturing the styrene heads and CNC cut tops and bottoms. Documentation of these processes can be seen below.
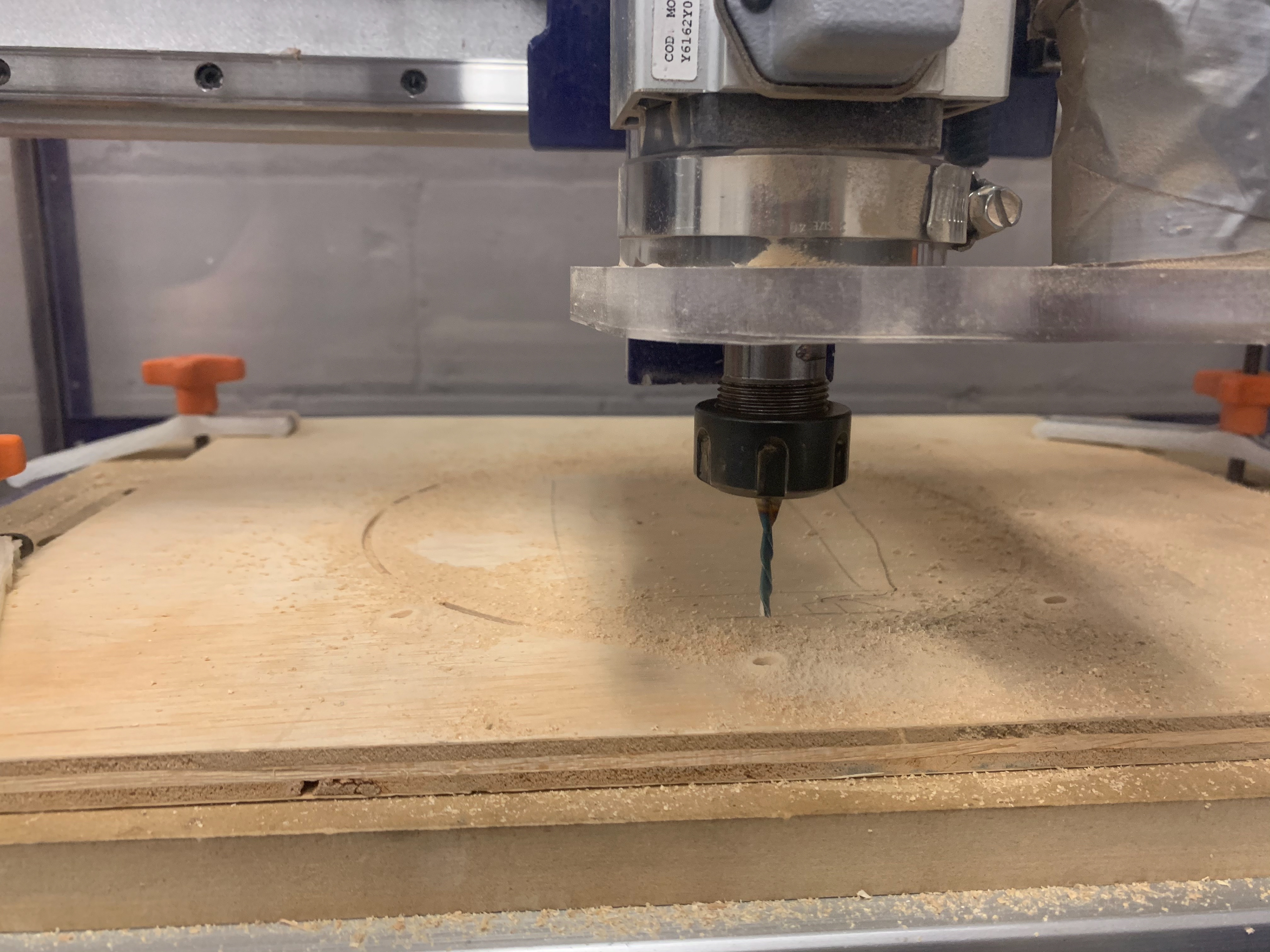
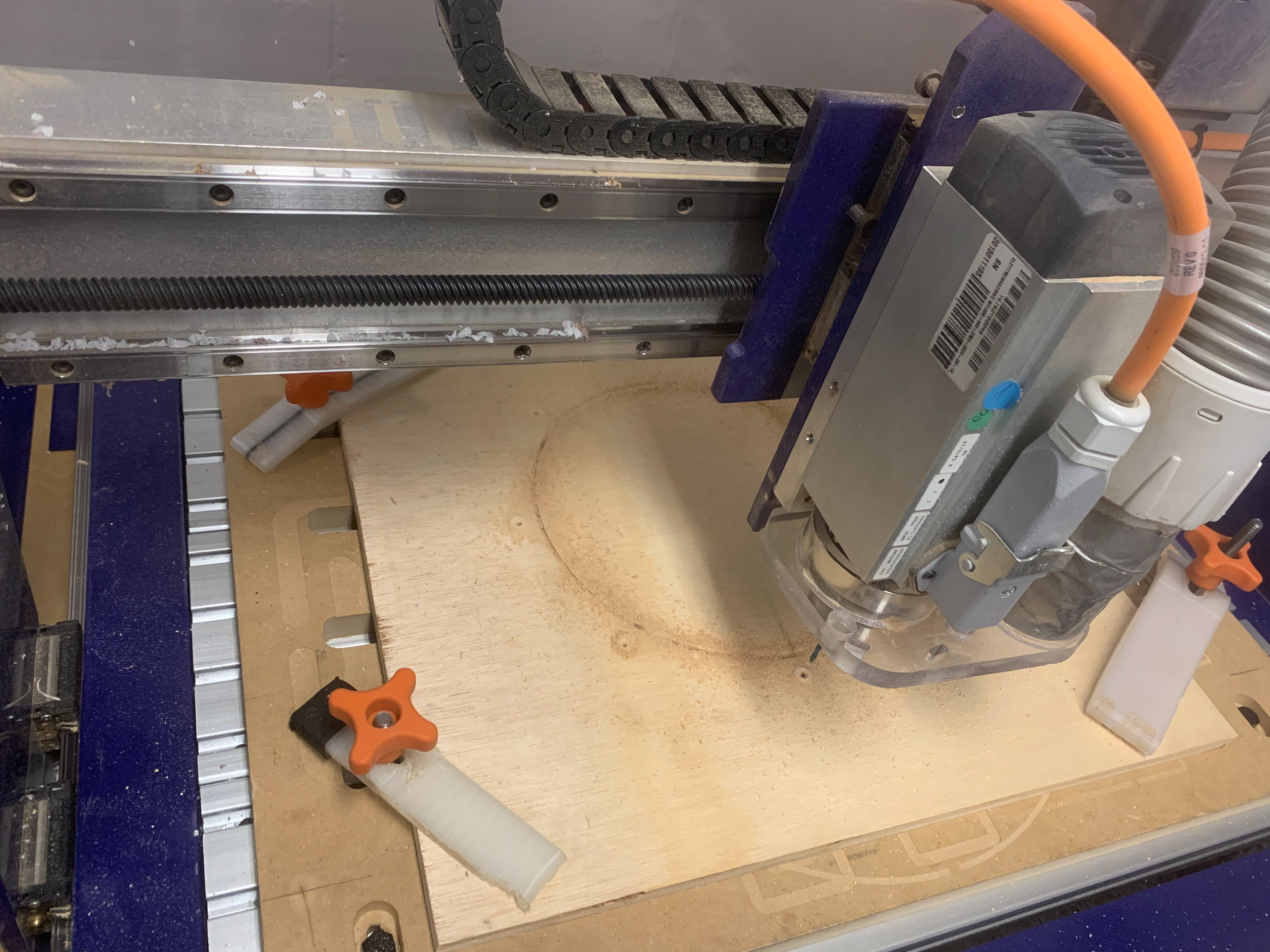
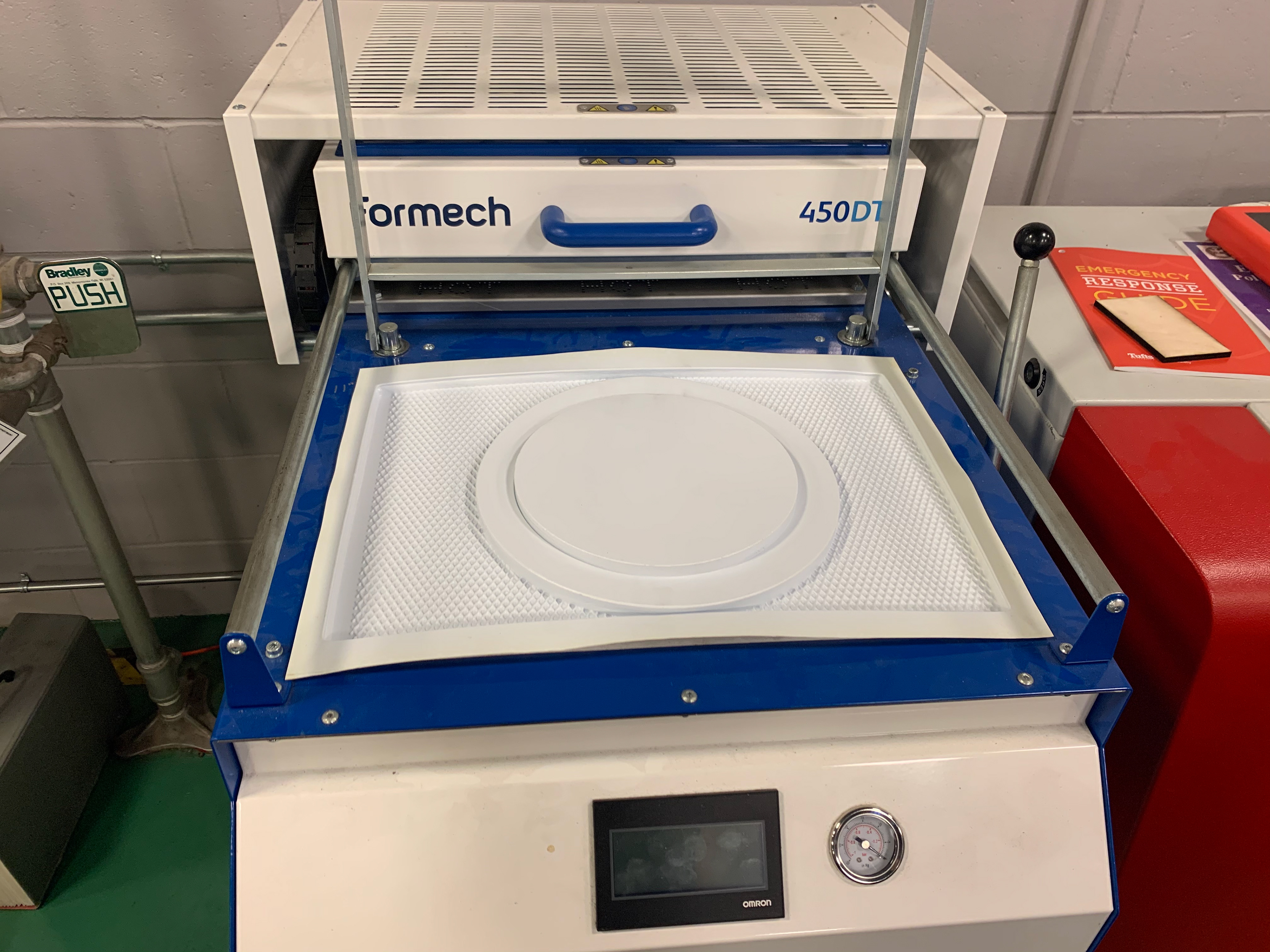
Once the main components were fabricated, my partner and I ran into a challenge in how we were going to successfully bend a plywood sheet into the spacing ring. After going over to the maker space and asking around, we found that the MAKE club had purchased a steam generator, which had gone unused until this time.
After cutting the wood strip to size, we hooked the steam generator into a PVC pipe creating a steambox. Photos of the steambox can be seen below.
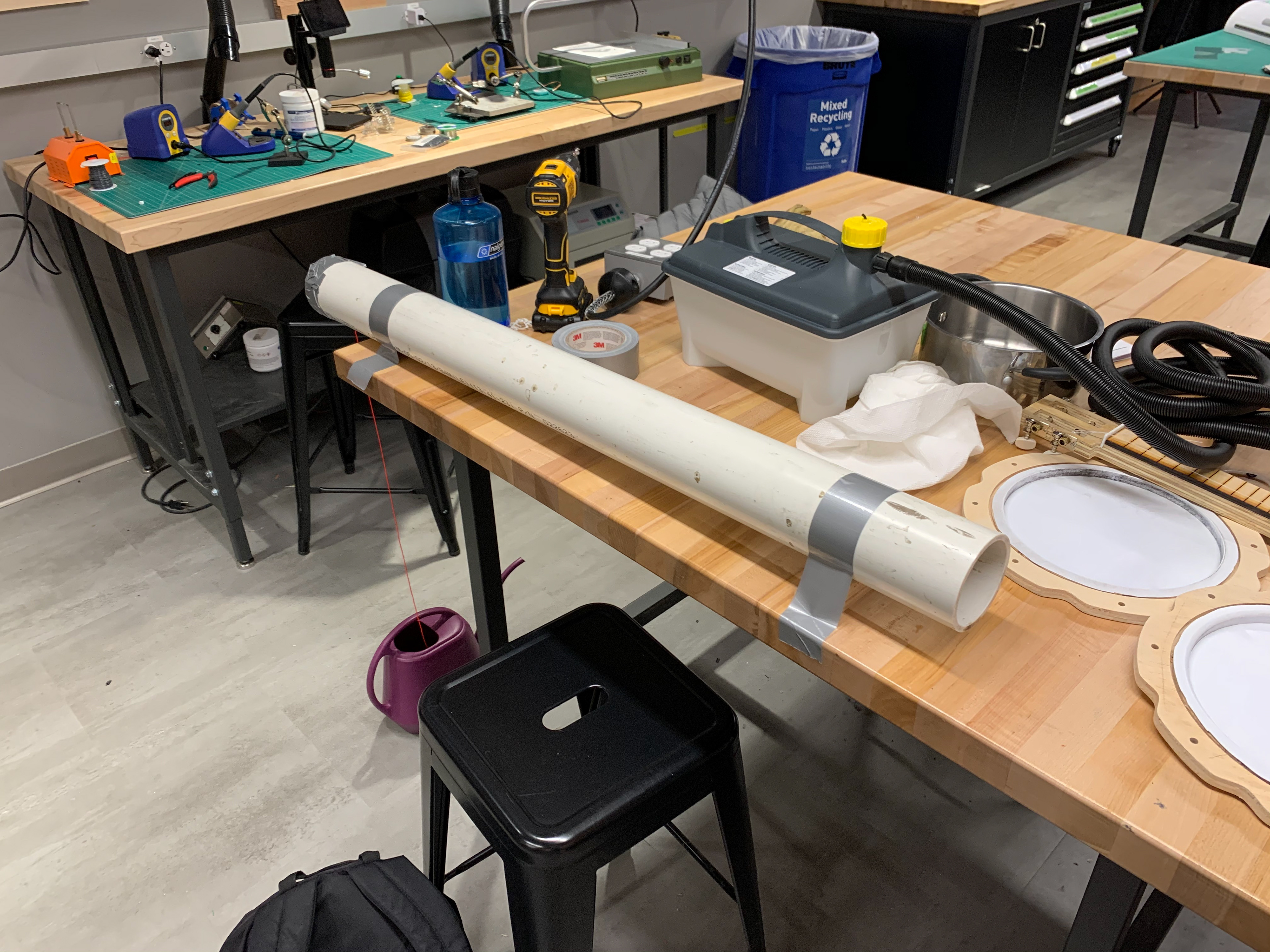
The steaming process took about 30 minutes, but after a full cycle the plywood was completely malleable and ready to be bent.
When designing the bottom and top faces of the ukulele, I put a register alignment groove inside the lip that allowed us to use for bending the plywood into the faces.
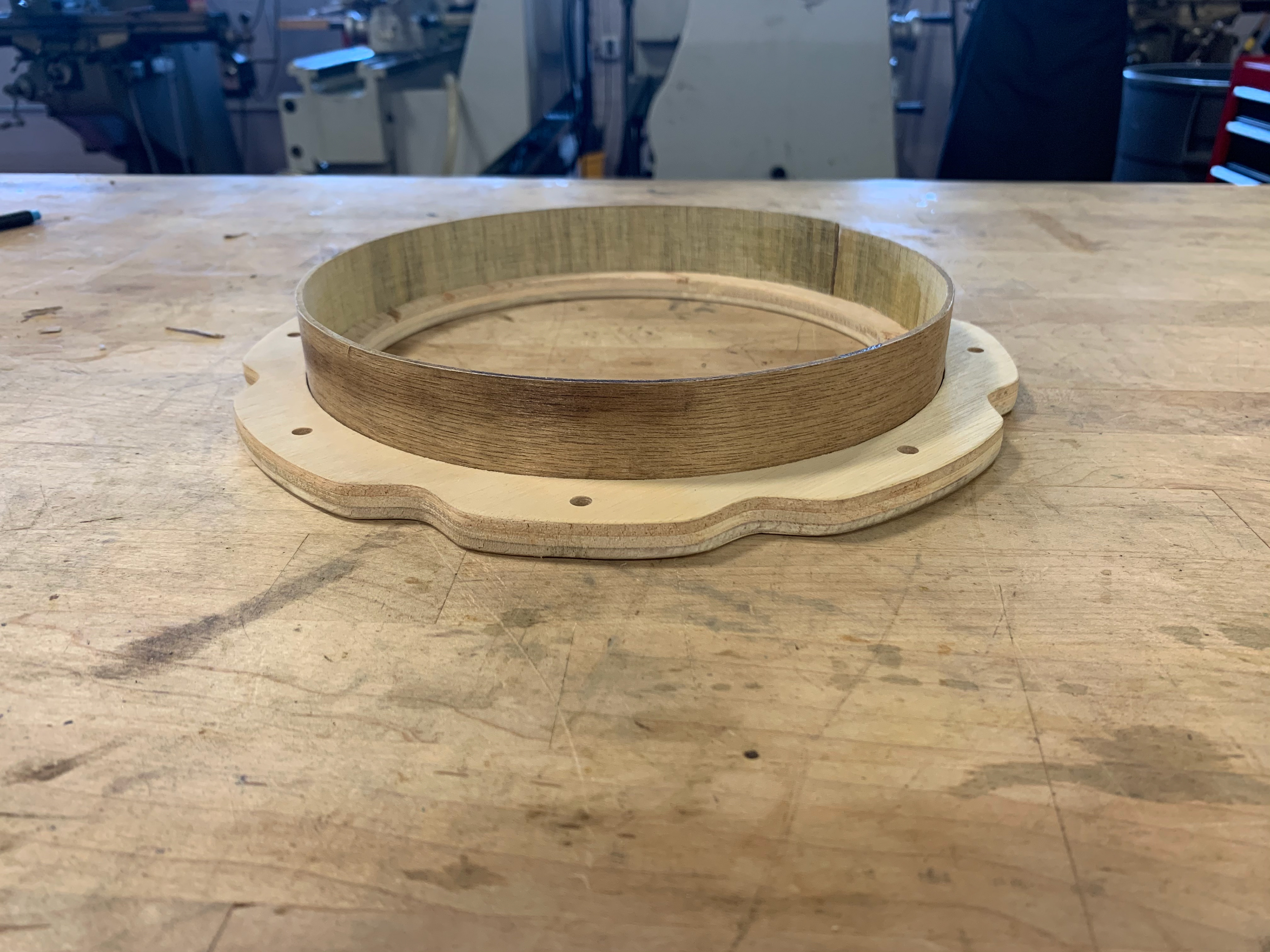
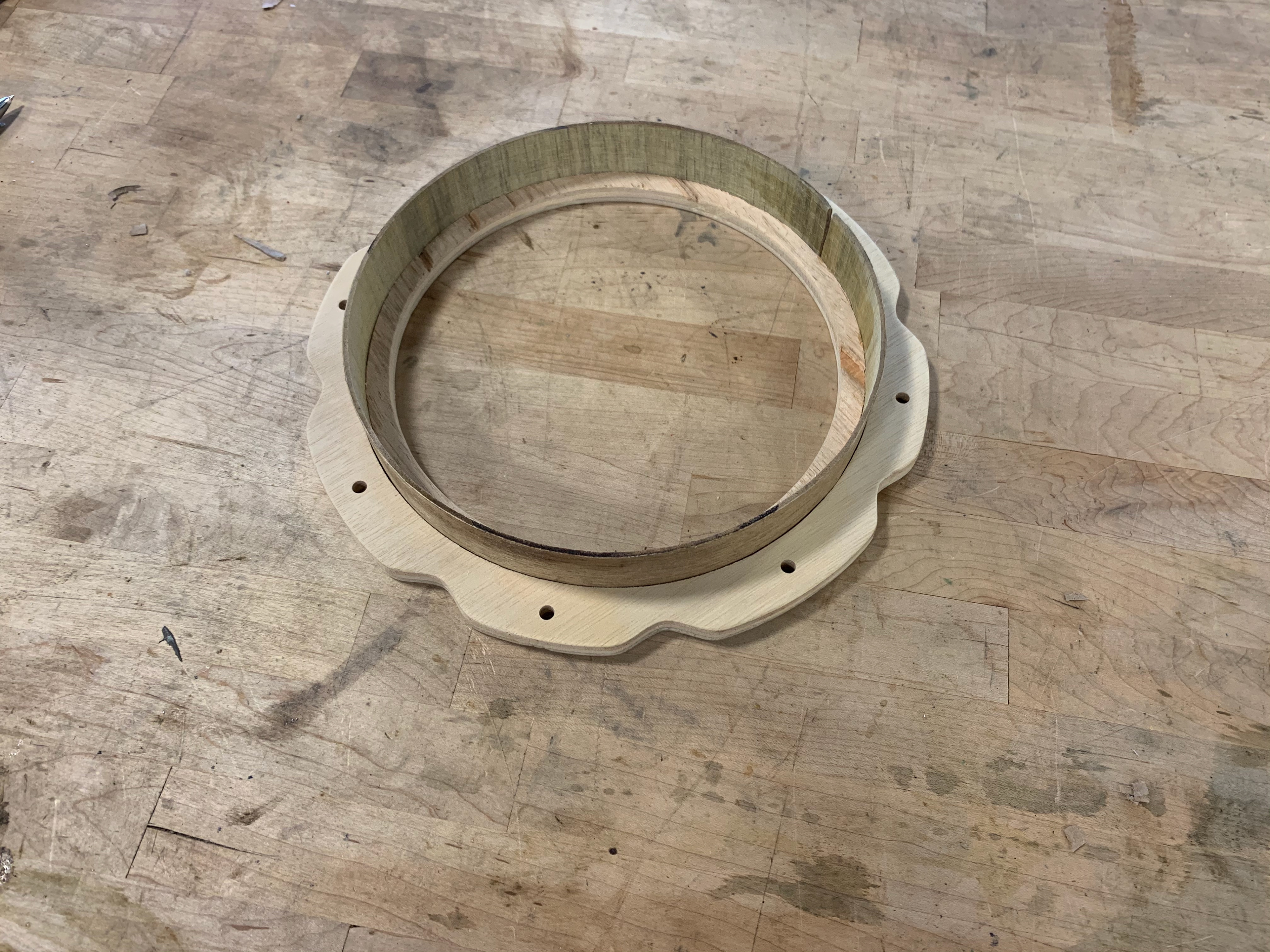
After mocking the whole assembly up, the final resonating chamber stack up is shown below.
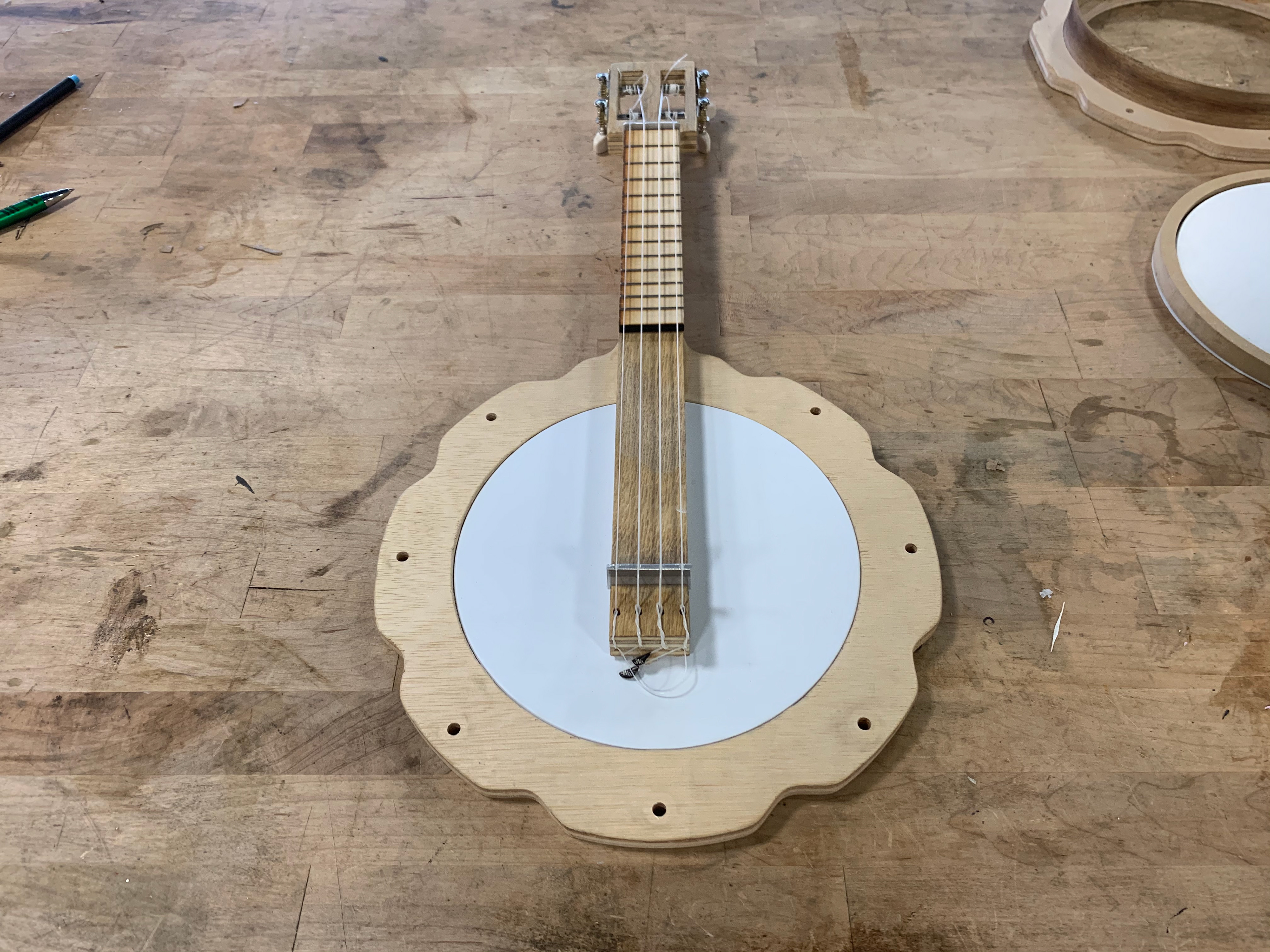
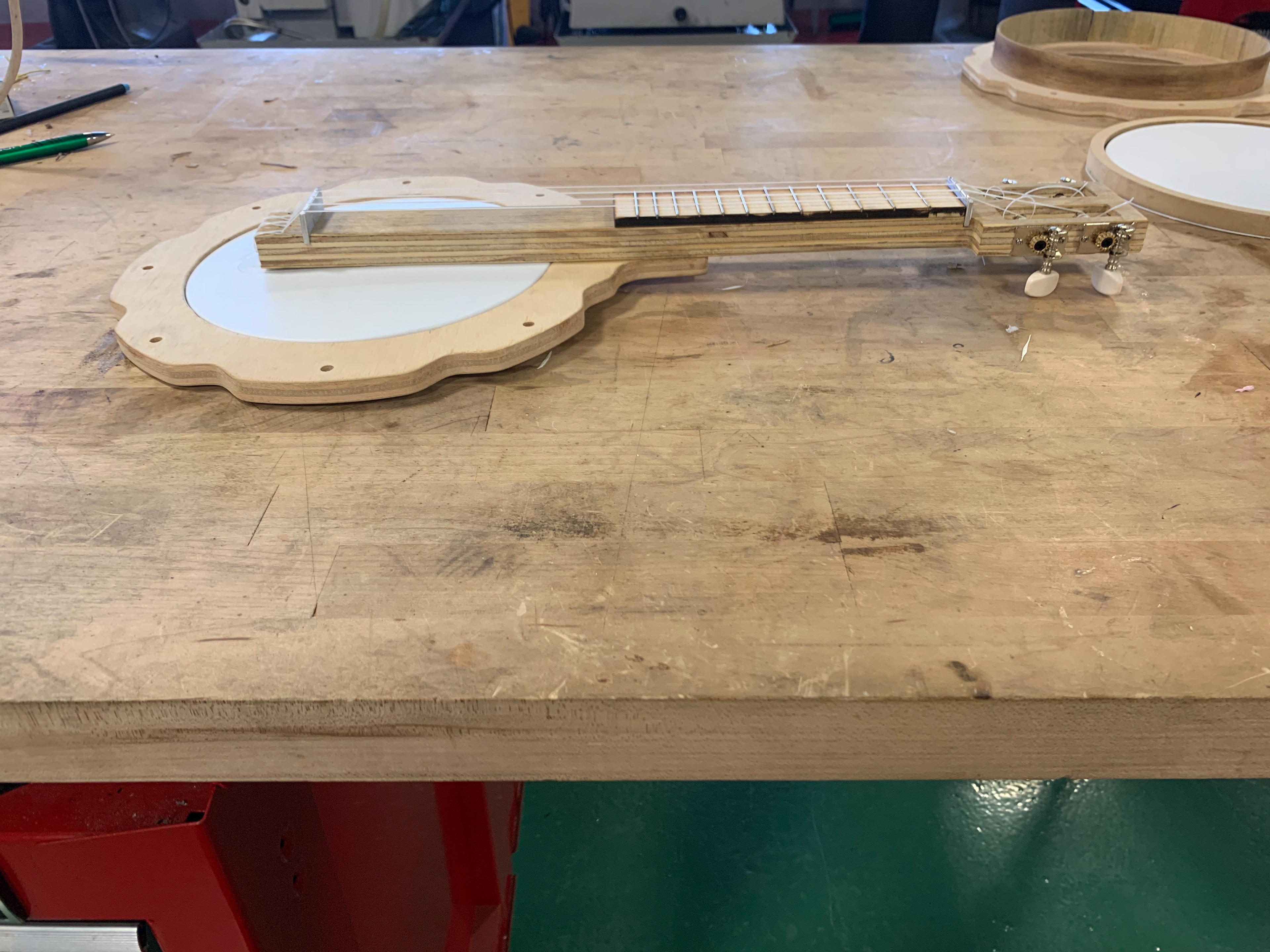
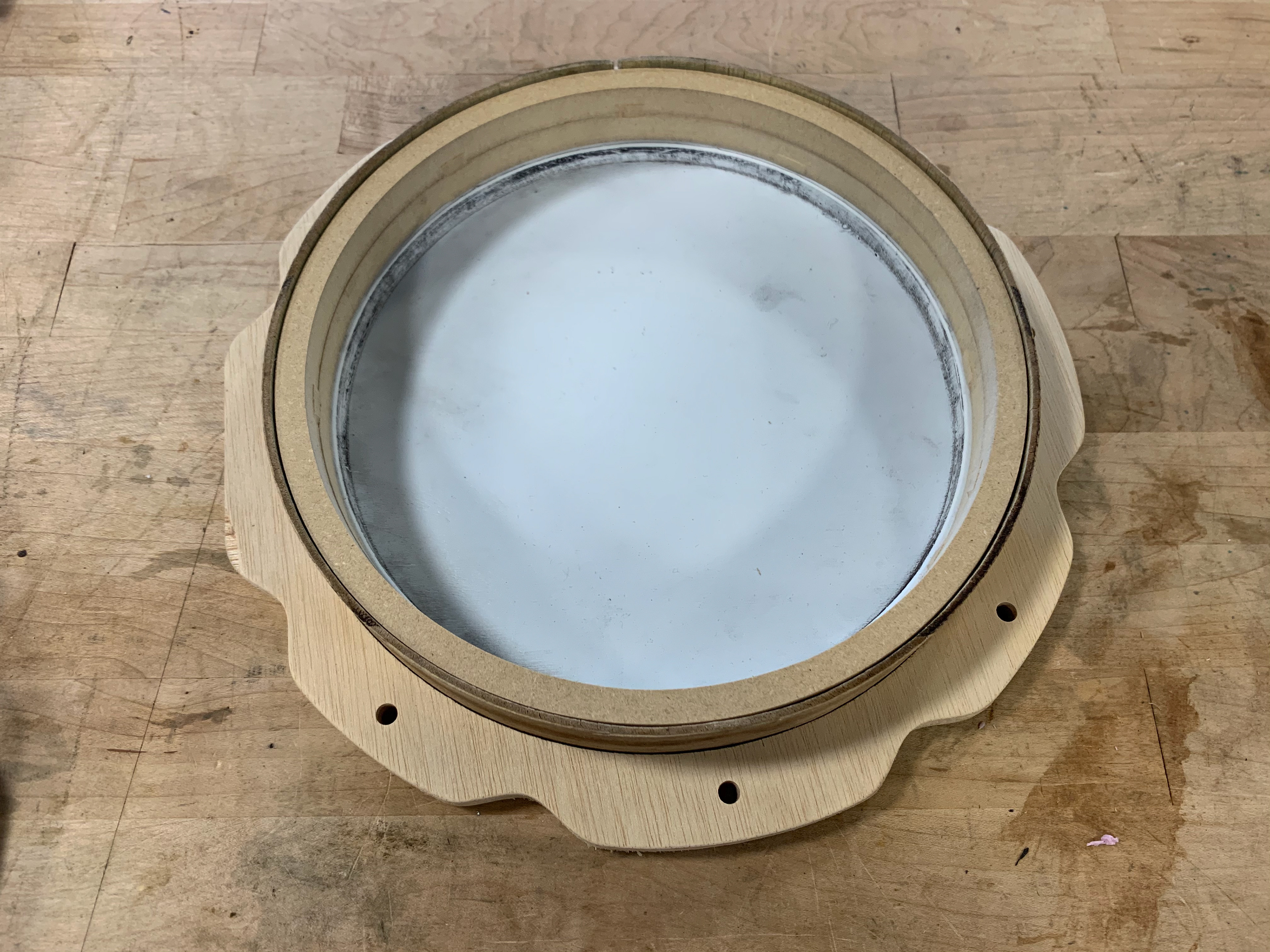
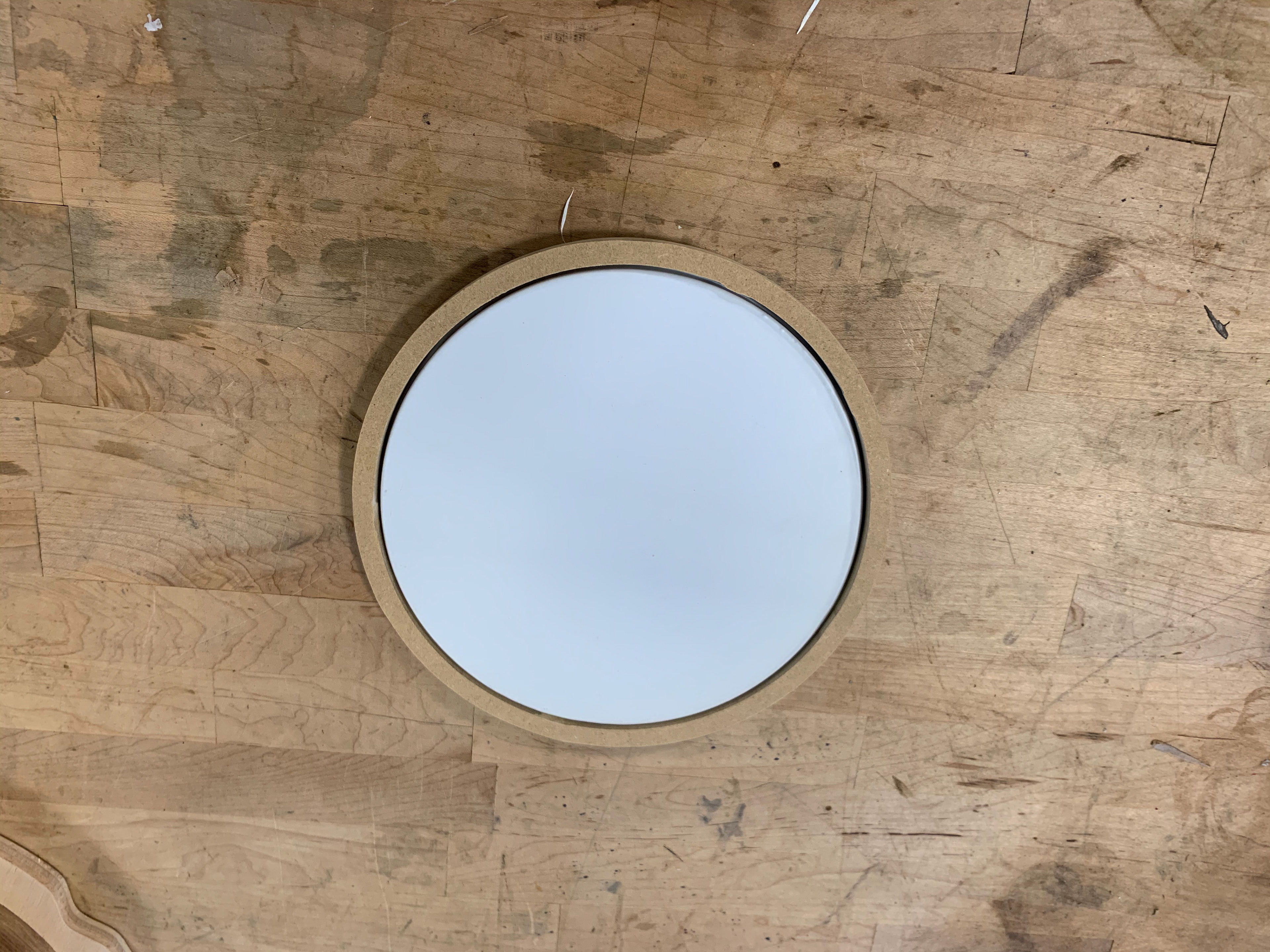
One of the design considerations that we came to was to not utilize any adhesives on the body assembly, only on the neck to body joint for consistent vibration transmission from the strings
Instead we opted to mimic the head tensioning bolts of a traditional banjo and secure the stack-up with seven bolts holding the assembly in constant compression. This compression allowed for irregular forming the styrene to become pulled out and tension the banjo heads like head of a drum.
After attaching the neck the final stages of the build entailed fabricating the aluminum nut and bridge and shaping the neck the of Banjolele.
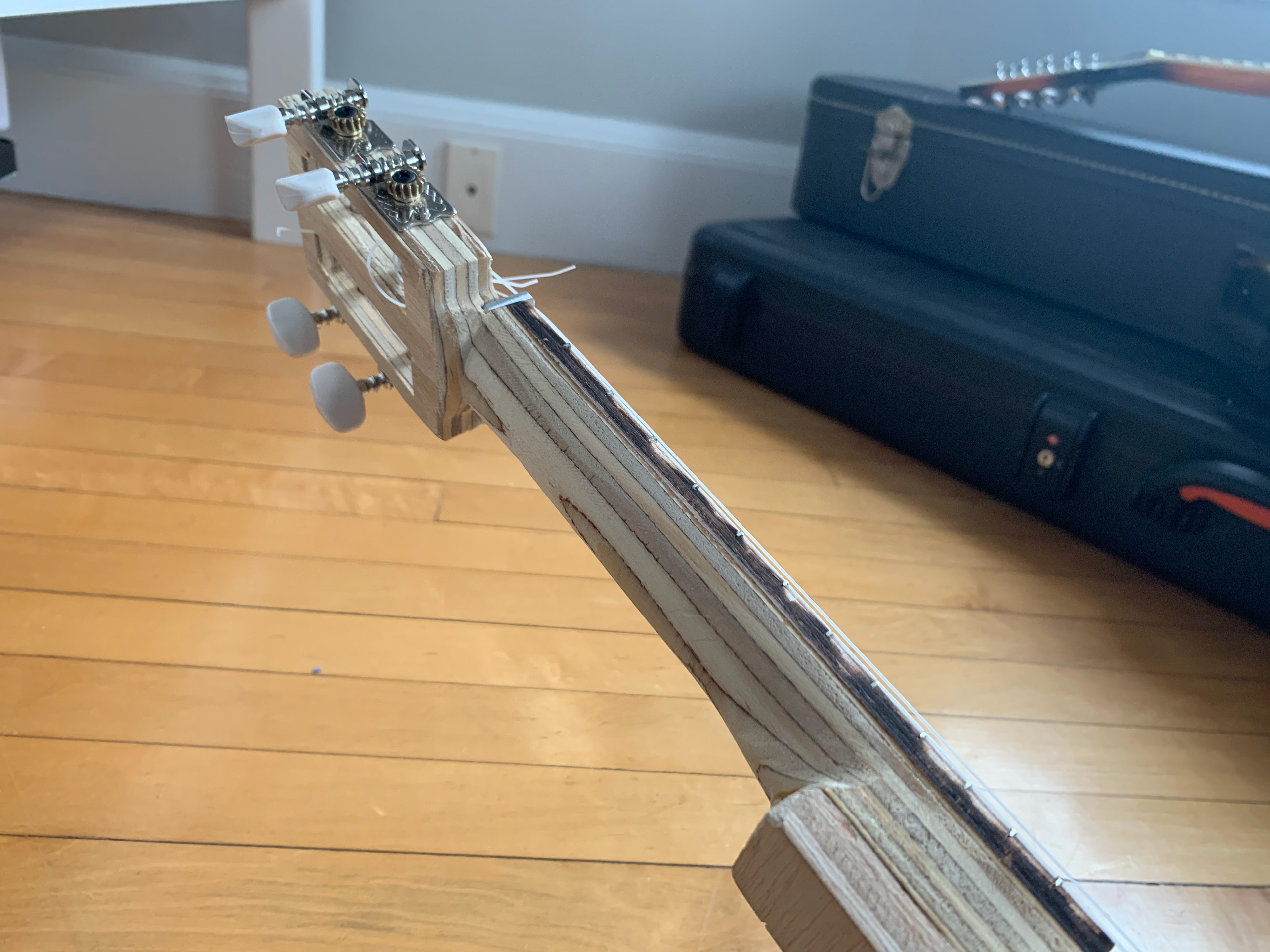
After initial response testing, the Banjolele performed well but due to the tension of the top and bottom faces the neck floated above the resonating chamber making the only point of vibration transmission through the heel connection point. This was simply remedied with a small shim placed under the neck which greatly increased the response of the instrument.
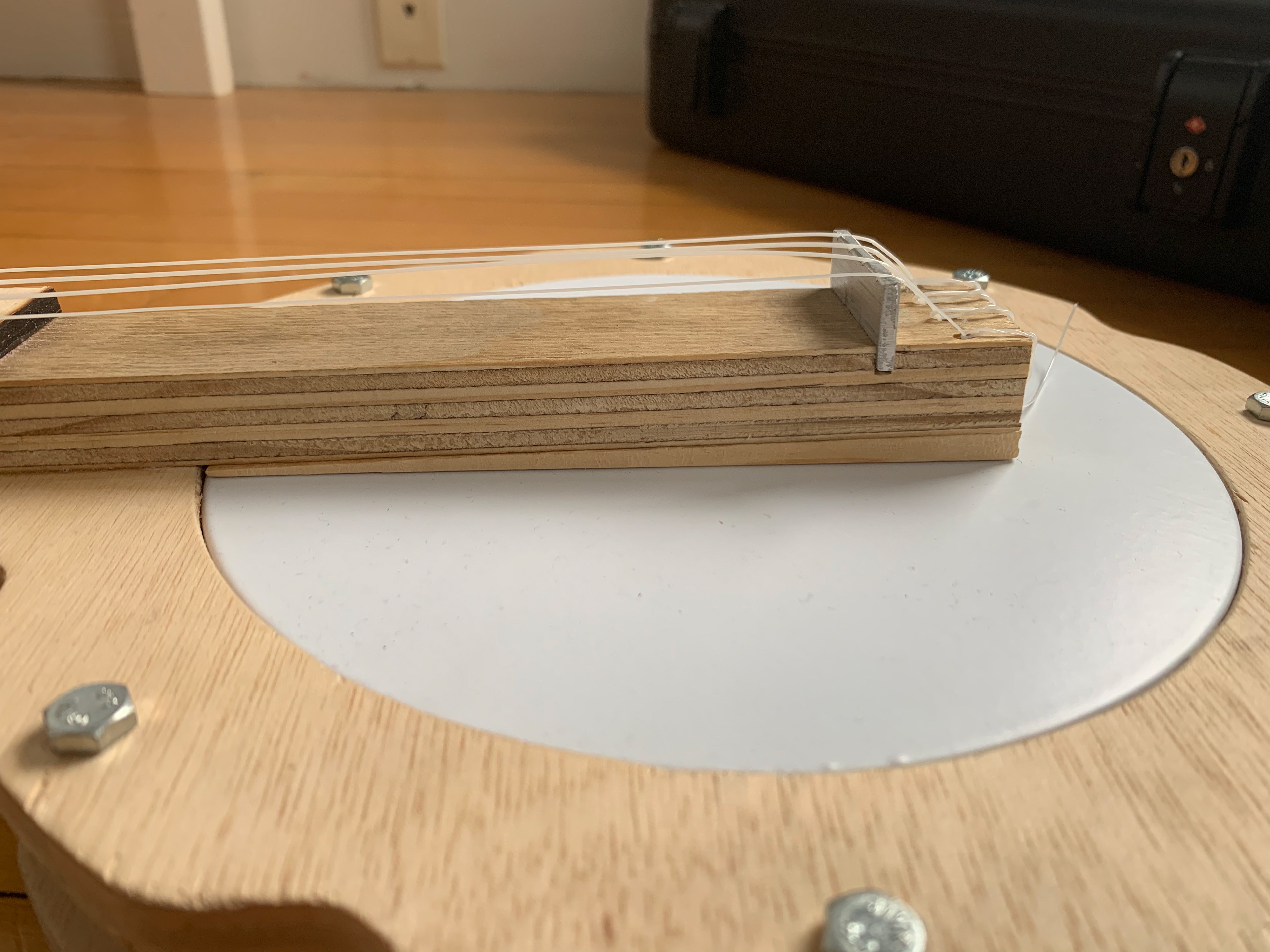
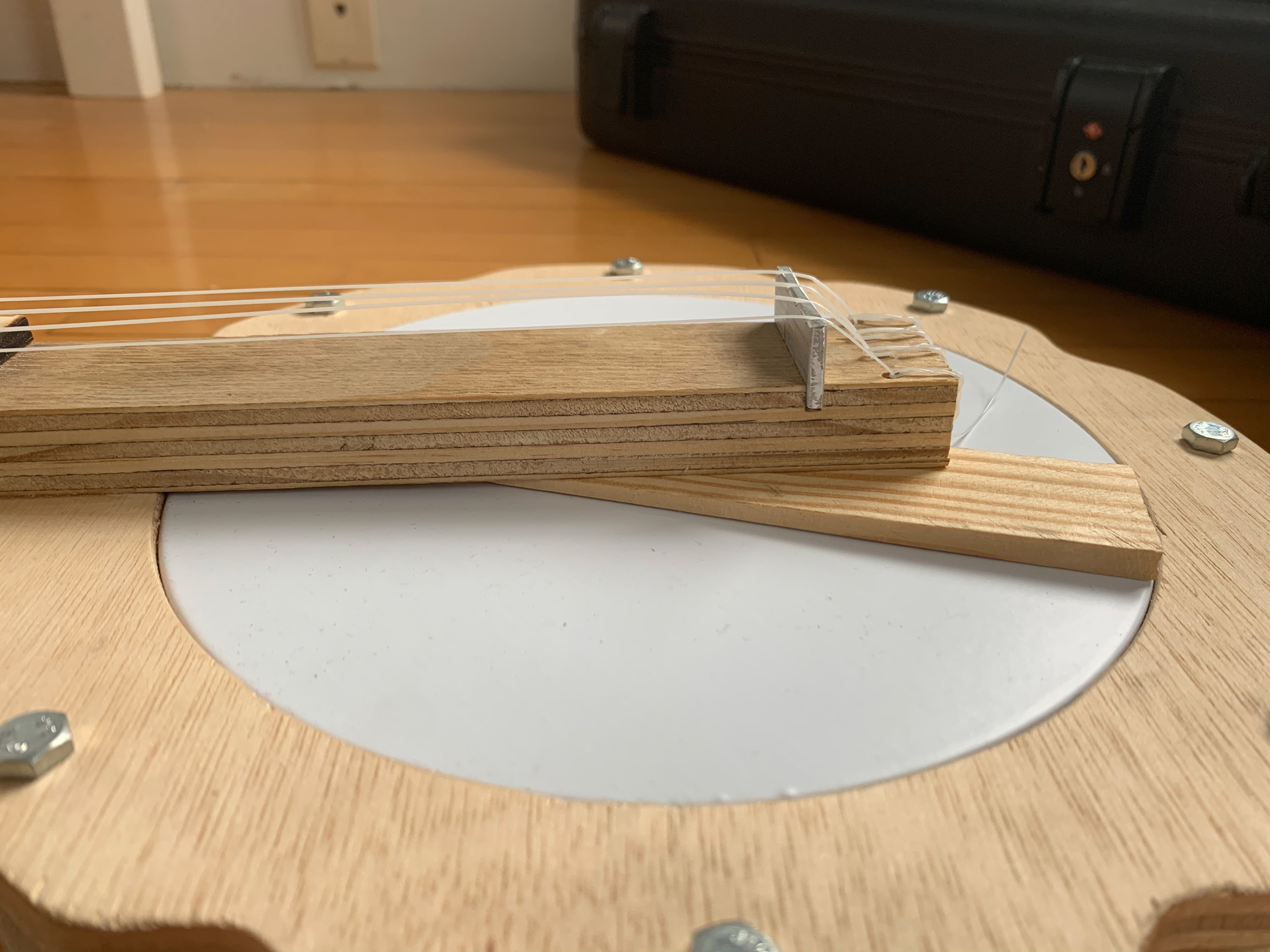
The final result of the design process of the Banjolele can be seen below.
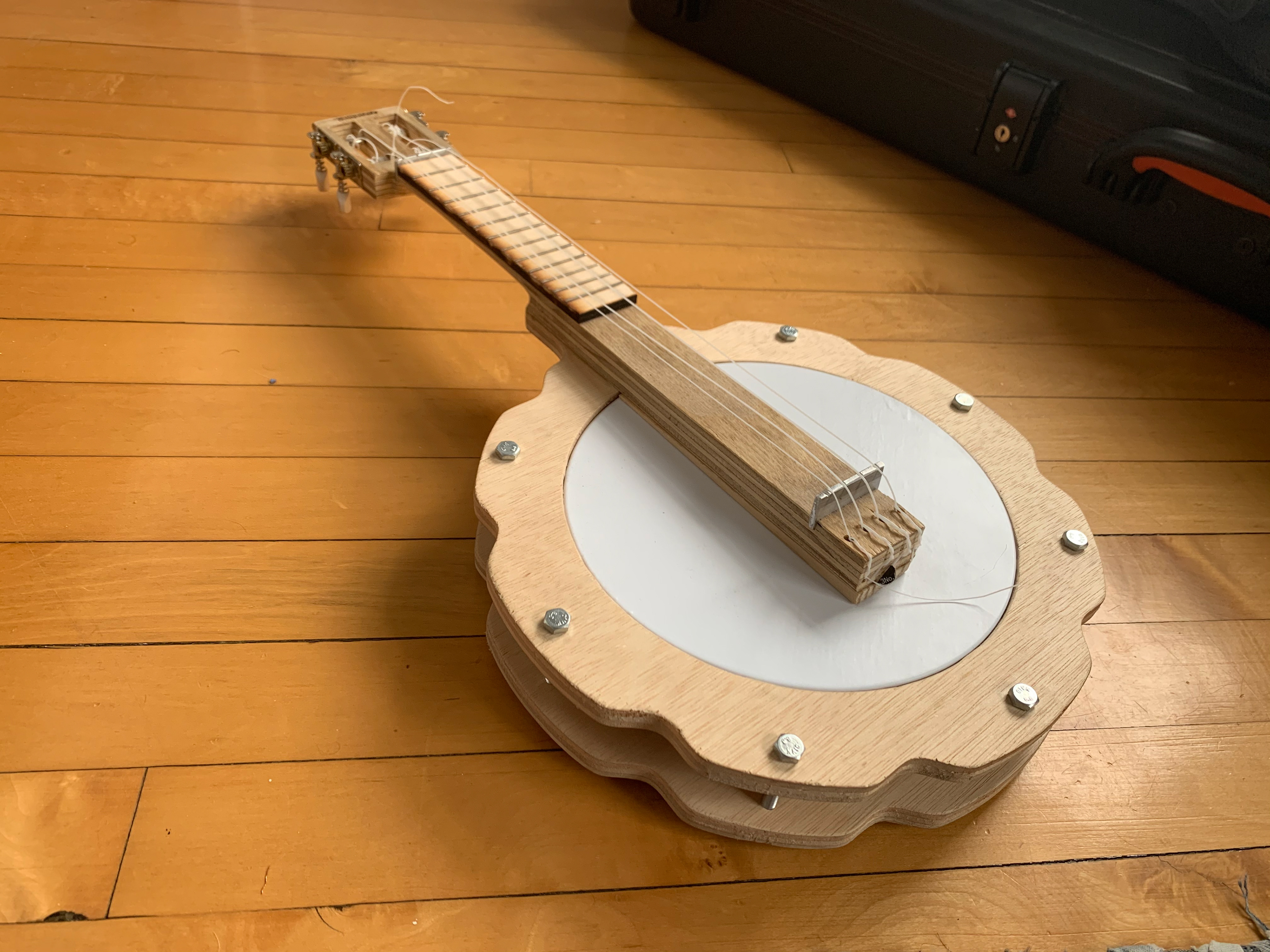
The final touch was added to the instrument with the use of the Trotec Laser Cutter
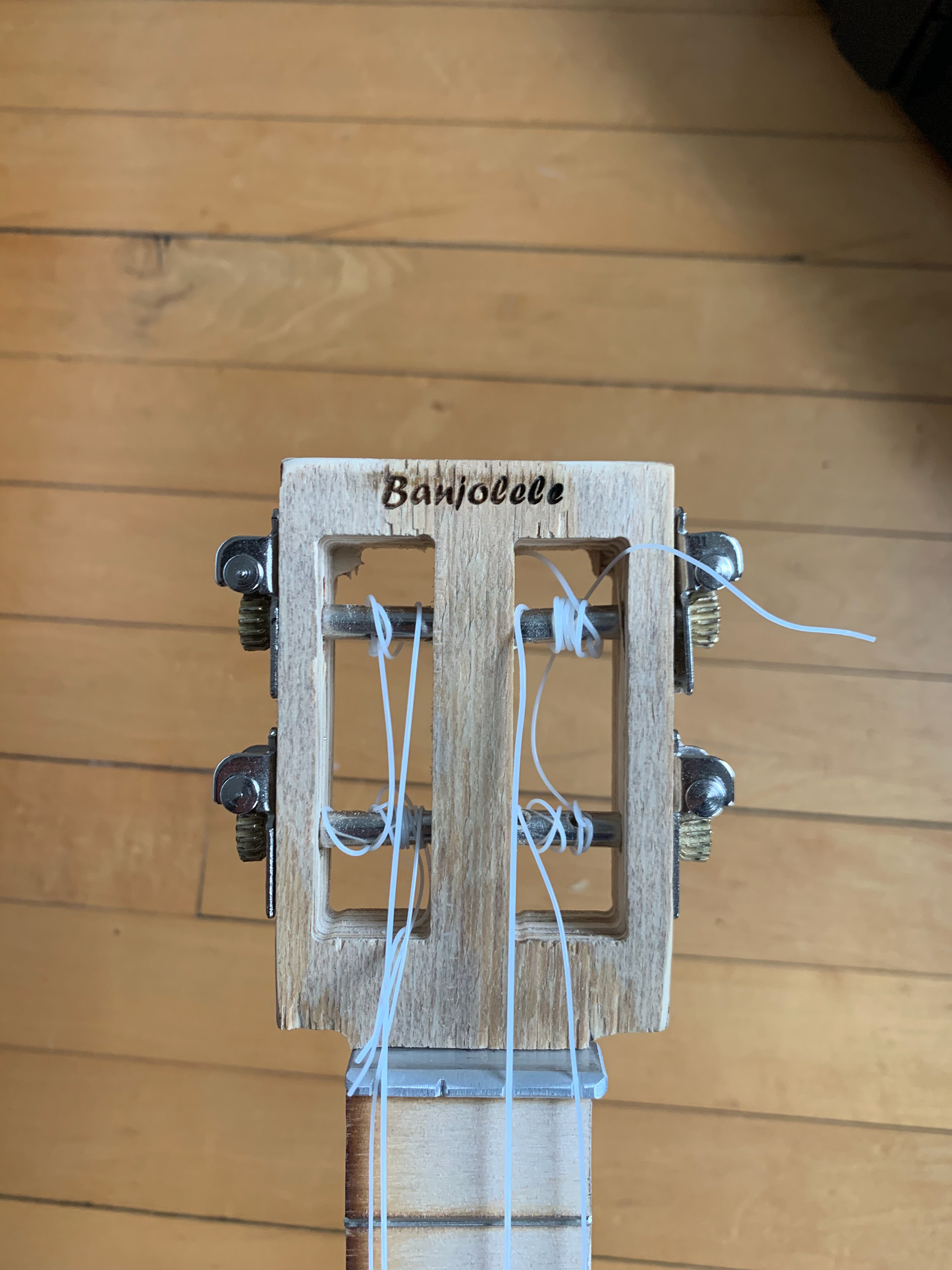